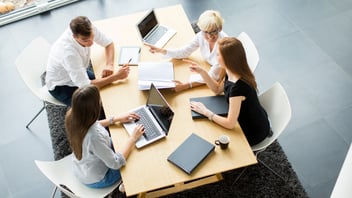
Why do Australians need to work harder at 'Working Smarter'?

Michael Kazoglou, a Senior Associate at Institute for Lean Systems (ILS) will share recent global thinking and developments in the areas of Operational Excellence as it relates to the Australian landscape.
In this article I aim to share some operational excellence thoughts and insights, particularly from my years working and being exposed to several hundred operations within a number of industries locally and overseas.
During my early days at Toyota my Japanese sensei asked me a question: What is the purpose of the Toyota Way (Lean)? Before I tell you how I answered I have a few questions for you:
-
Why do we (Australians) need to work harder at ‘Working Smarter’?
Recently, I had the pleasure of working as a global consultant, based in Europe for the Dutch affiliate of the Lean Enterprise Institute (LEI). Working in The Netherlands, which has a population of around 17 million, I could drive for four hours and travel across most of the country. In such surroundings, your business could supply organisations with products or services quite easily when contrasted with the geographical barriers in Australia. It was my observation that European organisations are not more efficient but still quite profitable. In Europe, you are also surrounded by endless influences that help to develop you including: many forms of innovation and new technology; best practices in many fields; environmental leadership and so on.
My various roles have allowed me to expand my insights into ‘what good organisations look like’ outside of Australia. My first exposure to true ‘World-Class’ operations was in 1996, with my first study visit to Toyota Motor Corporation Japan, to be taught by the founders of Lean Management system. Still to this day, very few organizations are able to match the organizational performance of the best Japanese companies back then; in many industries we (Australians) continue to fall behind the rest of the World. Many operations excellence programs do not reach their full potential and would like to challenge you to reflect on how we could work harder at ‘working smarter’.
- Does your organisation’s Operational Excellence or Organisational Improvement strategy enable breakthrough transformation throughout all areas of your organization?
Most organizations will have a form of continuous improvement (CI) program. However, many organisations will not appreciate the impact it (CI) could have strategically across all areas of their organization. We too often find that improvement programs are not adequately structured or supported at the most senior levels.
One of my Japanese coaches once told me that ‘you don't delegate your transformation program’. The transformation ‘leader’ must be personally involved and provide a commitment, not simply a contribution. There is an analogy for this: “at a breakfast of bacon and eggs, the chicken has made a contribution, but the pig has made a commitment”. I am not suggesting that our leaders follow the pig’s example exactly, but I think you get the point. I would like to clarify a key point; the most senior leader must drive the transformation plan strategically, however it is the ‘Line Manager’ who owns that transformation - they will however need support. I would suggest you also review the problem solving credentials of your leaders and internal improvement personnel, and design plans to support their development.
One of my clients in Italy, rated as one of the best lean organizations in the country, established long-term partnerships with external coaches, even after more than a decade of industry leading transformation. Additionally, they build internal improvement expertise by conducting improvement events every two weeks. These are lead by senior staff and everyone in the company participates as they tackle problems across the organization. Here lies the heart of where most organisations miss the ‘silver-bullet’ of transformation – develop your teams!
Improvement programs are most effective if the best performers are dedicated to the process, they are supported at the most senior ranks, and projects are focused on the strategic organizational challenges. Seeking very experienced external improvement coaches for advice on transformation structure, direction and people development is strongly recommended (this is not a sales pitch!). So, how would you rate your commitment to your organization’s transformation process?
-
What is Lean? Why Lean?
Just in case you may not be familiar with the Lean improvement methodology, there is an endless list of sources where you can find a definition.
What is Lean?
A conventional definition from the Lean Lexicon:
A business system for organizing and managing product development, operations, suppliers, and customer relations that requires less human effort, less space, less capital, and less time to make products with fewer defects to precise customer desires, compared with the previous system of mass production.
The key lies in what missing from this definition; in the ‘how’, not the ‘what’. How does lean really deliver such high levels of performance? How do organisations actually go about implementing a sustainable organisational transformation? The ‘how’ includes delivering this form of breakthrough performance by positively and proactively engaging everyone in the organization to become a problem-solver. Does your organization have an explicit goal of developing everyone into a problem solver?
-
Why use the ‘Lean Transformation (Model) Approach’ to achieve real breakthrough performance?
Lastly, I would like to introduce you to an exciting new transformation approach. This organisational transformation model can be applied in daily work or when implementing your improvement programs. John Shook, CEO of the Lean Enterprise Institute (LEI), the group that brought Lean to the world, can be seen on YouTube personally explaining the model. The model is structured by a series of five questions, which provide an insight into five success factors of any change process. The model uses a situational approach and is therefore practical – the lean goal is to not implement tools, but to solve specific business problems.
Lean Transformation Model (Lean Enterprise Institute, John Shook)
- What problems are we trying to solve?
- How will we improve the work?
- How will we develop the people?
- What leadership behaviors and management system are required?
- What basic thinking (mindset, assumptions) underline/drive this transformation?
This now brings me back to my original statement, and how I answered my sensei question: What is the purpose of the Toyota Way (Lean)? Back then I answered conventionally (i.e. the purpose is to improve quality & cost etc) and I was wrong. The answer my sensei was looking for was: the purpose of lean is to develop human resource capabilities and his will in turn deliver excellence. The answer lies within questions 3 and 4 in the model above.
“Toyota is in the business of making People. People make cars”
Toyota Motor Corporation.
By Michael Kazoglou, Senior Associate at Institute for Lean Systems (ILS)
Michael’s background in continuous improvement starting by being developed by the founders of lean principles at Toyota, when his team supported a numbers of supplier organisations. He then went onto lead the global CI program at Foster’s group and in the last two years has supported organisation in a consulting capacity in Europe and Australia.
Related
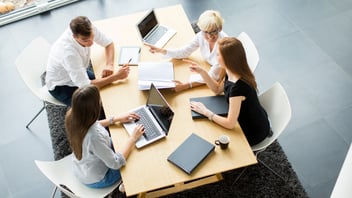
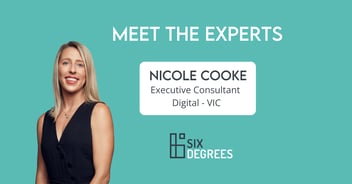
Meet the Experts: Nicole’s insights on the evolution of digital marketing
Welcome to our Meet the Experts series, where we spotlight the industry specialists at Six Degrees...
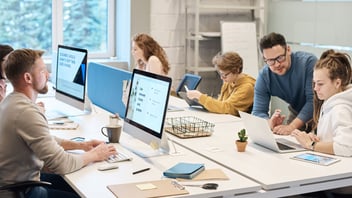
7 ways to revamp your EVP in 2025 to attract and retain talent
Gone are the days when office perks like foosball tables and free lunches were enough to attract...