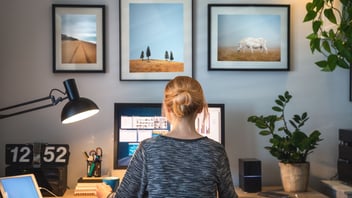
The Need for Effective Reactive Improvement

Ross Kennedy leads a discussion on how organisations can reach operational excellence utilising reactive and proactive improvement.
Many organisations get so focused on Pro-active Improvement through their Lean, Six Sigma, TPM etc initiatives that they lose sight of the importance of effective Reactive Improvement.
We often refer to Reactive Improvement as ‘below the line’ improvement as opposed to Pro-active Improvement which is ‘above the line’ improvement in relation to the daily budgeted performance expectation.
As Pro-active Improvement gains momentum and guides you closer towards Operations Excellence, then the need for Reactive Improvement should significantly reduce. However, as a Pro-active Improvement journey can take many years to achieve Operations Excellence, there is a strong argument for getting effective Reactive Improvement in place. This can be an effective means to achieve significant bottom-line gains very quickly at your site.
We have also found organisations that do both are the most successful especially if the focus of the Reactive and Pro-active Improvement activities are on the progressive on-going development of all people, so as to ensure long term sustainability of improvements
Effective Reactive Improvement is also a great foundation for accelerating your Pro-active Improvement activities.
What is Effective Reactive Improvement?
Reactive Improvement is your ability to rapidly recover from an event or incident that stops you from achieving your budgeted or expected performance for the shift or day and most importantly initiate corrective actions so that the event or incident will not re-occur anywhere across the organisation.
Reactive Improvement should be initiated whenever you fail to achieve expected performance based on agreed triggers eg greater than say 30 minute downtime or rework event or greater than 5% quality loss such as scrap or rework. The triggers should be initially set to allow the significant problems to be addressed within resource constraints. Obviously as the triggered problems become less and you become better at addressing them, you would reassess and tighten the triggers accordingly eg when 30 minute delays become less frequent you would reset the trigger to a lower figure like all delays greater than 15 minutes.
The key to effective Reactive Improvement is discipline through a very effective Daily Review Process supported by a standardised and robust Frontline Problem Solving process that is suitable for all people to be trained in, and used regularly, across the organisation.
Daily Review Process
Most organisations have daily review meetings however far too often they are not effective. What makes an effective Daily Review Meeting:
- Agenda displayed with clear timeframe for each agenda item;
- Current performance information is updated before the meeting by attendee responsible and displayed using visual prompts (eg red is bad, green is good);
- Stand up environment (no chairs as people think and respond quicker and more distinctly on their feet);
- Clock in room (visually controlling the time of meeting);
- Respect for People - Start and finish on time (allow people to leave after agreed finish time);
- Any deviation from expectation noted with solutions taken, or if issue has not been resolved, support is allocated to assist (to be resolved outside meeting);
- Triggers for activating a Frontline Problem Solving action are displayed and regularly updated;
- If a trigger for generating a Frontline Problem Solving A3 Summary Sheet is activated, then a Frontline Problem Solving action is allocated to a designated person with timeframe for reporting back (eg within 3 working days advise outcome of Step 4 – Develop Root Cause Solutions and proposed action plan); and
- Everyone leaves knowing their issues are going to be properly addressed and with clear expectations of required performance for at least the next 24 hours.
Frontline Problem Solving Process
There are many Root Cause Analysis problem solving processes in the marketplace however the key (as discovered by Toyota many years ago) is to find one that can be used by all people in an organisation rather than just a select few. In other words it needs to be simple and effective.
CTPM has developed a simple and highly effective 7 Step Frontline Problem Solving Process supported by an A3 Summary Sheet based on Detailed Problem Definition, Cause & Effect Analysis and Why-Why Analysis that is now being successfully used by many organisations at all levels with very good results.
A key learning in developing the process has been that having people attend a one-day or two-day workshop is a great way to introduce Frontline Problem Solving or Root Cause Analysis however to learn and gain confidence in a the process people need to successfully work through at least 3 separate problems preferably in a team environment using real and relevant incidents or events from their workplace.
As such we have found having a team or teams of 4-5 people attend a one-day workshop where the first problem is addressed to ‘identifying possible solutions’ stage then allowing the team to return to their workplace, verify or reinforce their analysis with further facts and data and implement their possible solutions over the following week is a great starting point. This should then be followed up with say 6 weekly team meetings of 1-2 hours to allow each team to progress their first problem and address another 2 recent incidents or problems.
Typically after successfully completing 3 incidents or problems within a team environment, each person should be ready to tackle problems or incidents raised at your daily review meetings by themselves. We would expect they would call upon work colleagues to assist where necessary along with having access to your trained in-house nominated facilitator if and when required to ensure the quality and robustness of their analysis.
By Ross Kennedy – President, CTPM Australasia
For more information about CTPM’s approach to Reactive Improvement or Frontline Problem Solving please contact Ross Kennedy at CTPM’s Head Office on +61 4226 6184 or email: ross.kennedy@ctpm.org.au or visit CTPM’s web page.
Related
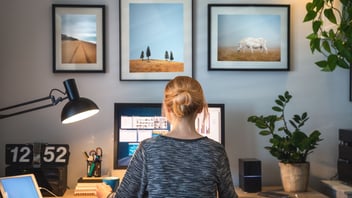
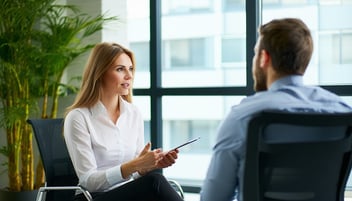
Overcoming imposter syndrome in interviews
Why do candidate struggle to “sell themselves” during an interview? What is the point of an...
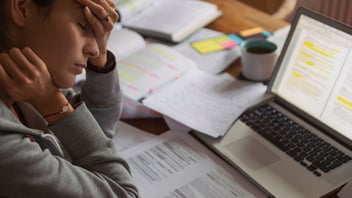
Understanding burnout – why it matters and what to do about it
Most of us understand the importance of taking time off work when we’re physically unwell or...